Gate Valves 101: Key Factors to Consider for Optimal Performance
Gate valves are a crucial part of many industrial systems, used primarily for the on/off control of fluid flow.

Gate valves are a crucial part of many industrial systems, used primarily for the on/off control of fluid flow. These valves are simple yet effective, and their performance is essential in a wide range of applications, from water treatment plants to oil and gas pipelines. Understanding the key factors that influence the performance of gate valves will help you choose the right valve for your needs and ensure that it operates efficiently over time.
In this detailed guide, we will explore the critical aspects of gate valves, including their types, design features, materials, maintenance, and troubleshooting tips. By the end of this blog post, you'll have a thorough understanding of gate valves and be better equipped to make informed decisions about their use in your systems.
What Are Gate Valves?
Gate valves are a type of valve used to control the flow of liquids and gases. The main function of a gate valve is to completely stop or allow the flow through a pipeline. These valves are designed with a gate or wedge that slides into the path of the pipeline to either obstruct or permit flow. When fully open, a gate valve offers minimal resistance, allowing the fluid to flow freely. When closed, it provides a tight seal to prevent leakage.
Types of Gate Valves
There are two main types of gate valves: rising stem and non-rising stem. Understanding the differences between these two types is crucial for selecting the right valve for your application.
-
Rising Stem Gate Valves:
-
In rising stem gate valves, the stem moves up and down as the valve opens or closes. This type is typically used in larger systems where the visibility of the stem position is important.
-
Pros: The position of the stem is visible, providing a clear indication of whether the valve is open or closed.
-
Cons: They require more space to operate due to the rising stem.
-
-
Non-Rising Stem Gate Valves:
-
Non-rising stem gate valves do not have a rising stem. Instead, the stem rotates within the valve body to operate the gate.
-
Pros: They are ideal for installations with limited vertical space, as the stem does not rise.
-
Cons: It can be more difficult to visually determine whether the valve is fully open or closed.
-
Key Components of a Gate Valve
To better understand how gate valves work, let’s take a look at their primary components:
-
Body: The outer casing that houses all internal components and connects the valve to the pipeline.
-
Gate (or Wedge): The element that blocks or permits the flow of fluid.
-
Stem: The part that moves the gate.
-
Seat: The surface that the gate seals against when the valve is closed.
-
Bonnet: The part that covers and protects the valve stem and provides a means for stem adjustment.
Important Factors to Consider for Optimal Gate Valve Performance
1. Material Selection
The materials used in the construction of gate valves significantly affect their performance and longevity. Gate valves are typically made from materials like:
-
Cast Iron: A common material used for gate valves due to its durability and cost-effectiveness. It is often used in water distribution systems.
-
Stainless Steel: Ideal for applications where resistance to corrosion and high temperatures is essential, such as in chemical processing or oil and gas pipelines.
-
Brass: Typically used in smaller valves, brass offers a good balance of strength, corrosion resistance, and cost.
The material you choose should be compatible with the type of fluid in your system. For example, if you are dealing with corrosive liquids, stainless steel or other alloys may be required for better protection against corrosion.
2. Valve Size
The size of the gate valve plays a crucial role in its performance. It should be appropriately sized to match the diameter of the pipeline to ensure proper flow regulation. The valve size should be chosen based on the flow rate requirements and the pressure within the system. Incorrectly sized valves may cause flow restrictions, poor sealing, or even system failure.
3. Pressure and Temperature Ratings
Every gate valve has a specific pressure and temperature rating, which defines the maximum pressure and temperature that the valve can handle safely. It is crucial to choose a gate valve that meets or exceeds the pressure and temperature requirements of your system. For instance, high-pressure systems require gate valves made from durable materials that can withstand extreme conditions.
4. Gate Valve Seals
The seals in a gate valve are vital to ensure leak-free operation. Over time, seals can degrade due to factors like temperature changes, chemical exposure, and wear and tear. Gate valve seals can be made from various materials, including elastomers, PTFE (Polytetrafluoroethylene), and metal seals. The selection of seal material should be made based on the application’s temperature and chemical requirements.
Common Seal Materials:
-
Rubber: Often used in general-purpose applications, rubber seals provide a tight seal and are flexible.
-
PTFE: Known for its high chemical resistance, PTFE seals are commonly used in aggressive chemical applications.
-
Metal: Used for high-temperature or high-pressure applications, metal seals provide a robust solution for extreme conditions.
5. Flow Direction
Gate valves are typically designed to control flow in one direction, but some models are bi-directional. When installing a gate valve, it’s important to ensure the valve’s flow direction matches the system’s flow requirements. Installing a gate valve in the wrong direction may lead to leaks and inefficiencies.
Maintenance Tips for Gate Valves
Gate valves require regular maintenance to ensure optimal performance. Proper maintenance can extend the life of the valve, prevent leaks, and reduce the risk of failure. Here are some essential maintenance tips:
1. Regular Inspection
Perform routine inspections to check for signs of wear or damage to the valve components, including the stem, gate, and seals. Look for corrosion, cracks, or any other physical damage that might affect the valve’s performance.
2. Lubrication
Gate valves with a rising stem should be lubricated regularly to prevent wear and ensure smooth operation. Lubrication helps to reduce friction between the stem and the valve body, preventing issues like jamming or difficulty in operation.
3. Cleaning
Clean the valve and its components regularly, especially when dealing with fluids that may cause buildup or clogging. Keeping the valve clean ensures that it operates efficiently and reduces the chances of failure.
4. Seal Replacement
Seals degrade over time, and replacing them before they fail can prevent leaks and costly repairs. Check the condition of the seals and replace them if necessary.
Troubleshooting Gate Valve Issues
While gate valves are relatively simple to operate, they may encounter issues that impact their performance. Here are some common problems and how to address them:
1. Leakage
If a gate valve is leaking, it may be due to a worn-out seal, damage to the valve body, or improper installation. To fix this issue, inspect the valve for any visible damage, and replace the seals if necessary. Ensure the valve is installed correctly, with the appropriate pressure and flow settings.
2. Sticking or Jamming
Gate valves may become stuck due to debris or corrosion. Regular cleaning and lubrication can help prevent this issue. If the valve is jammed, inspect the stem and gate for signs of obstruction or wear.
3. Difficulty Opening or Closing
If a gate valve is difficult to operate, it could be due to an issue with the stem or the actuator. Check for any damage to the stem, and ensure that the actuator is functioning correctly. Lubricating the stem can also help resolve this issue.
Frequently Asked Questions (FAQs) About Gate Valves
What is the difference between a gate valve and a ball valve?
Gate valves are designed to fully open or fully close the flow, while ball valves provide a more precise control of flow and are typically used for throttling applications. Gate valves are ideal for on/off applications, whereas ball valves offer better flow regulation.
Can gate valves be used for throttling?
Gate valves are not recommended for throttling purposes, as they are designed for fully open or fully closed positions. For throttling applications, ball or globe valves are typically used.
How can I tell if a gate valve is working properly?
Regular inspections are key to identifying potential issues. Look for signs of leakage, check the position of the valve stem (for rising stem models), and ensure that the valve operates smoothly without obstruction.
What are the most common causes of gate valve failure?
Common causes of gate valve failure include worn-out seals, corrosion, debris buildup, and improper installation. Regular maintenance and inspections can help prevent these issues.
Conclusion
Gate valves are essential components in various industries, and understanding their operation, design, and maintenance is crucial for ensuring optimal performance. By considering factors such as material selection, size, pressure and temperature ratings, and regular maintenance, you can ensure that your gate valve performs efficiently and reliably over time.
Choosing the right gate valve for your application, performing routine inspections, and addressing potential issues proactively will extend the life of the valve and prevent costly repairs. Whether you're installing a gate valve in a residential, commercial, or industrial system, understanding its function and maintenance needs will help you make the best choice for your specific requirements.
What's Your Reaction?

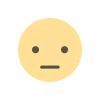




